THEORY OF OPERATION
The ultra sound sensors operate by transmitting a burst of high frequency sound waves and then measuring the amount of time it takes for the sound wave to reflect back to the receiver/transmitter. The frequency can be anywhere in the range of 20 KHz to above 100 MHz. The frequency is very application dependent. Ultra sound can be applied to operate in almost any medium; air, water (liquids) or various solid materials. It could be classified as a non-contact level system.
Ultrasonic Accuracy
The ultra sound sensors operate by transmitting a burst of high frequency sound waves and then measuring the amount of time it takes for the sound wave to reflect back to the receiver/transmitter. The frequency can be anywhere in the range of 20 KHz to above 100 MHz. The frequency is very application dependent. Ultra sound can be applied to operate in almost any medium; air, water (liquids) or various solid materials. It could be classified as a non-contact level system.
Applications:
Perhaps the most common use (from the general public’s point of view) is in sonography where pictures of fetuses in the human womb are generated. In the industrial environment, the use of ultra sound is generally used in two areas: 1) Ultra sound to detect flaws in materials; much like sonography, and 2) Measuring the level of a material within a tank or enclosure. These materials may be either a solid such as grains or a liquid such as fuels. Specifically, in a cooling tower, false level indications could occur when foam is present in the tower, turbulence in the basin causes reflections and in packaged tanks such as cooling towers the reflective nature of the walls.
Advantages:
The ultrasound is a non-contact method of measurement and is therefore isolated from the material being measured. Sensing using ultrasound can be further isolated by placing the transmitter in a totally sealed enclosure. Since contact is not a requirement, the material level measured can be of any type: solid, granular or a liquid of any viscosity. Hazardous materials are particularly suited to this method.
Disadvantages for water:
This type of sensor can be subject to spurious readings due to foaming action layers on the surface, the reflective nature of water, changes in the transitivity of the water between the sensor and the water being measured and standing waves or agitating water that can occur at specific distances between the sensor and the level being measured. There can be a “Dead” space up to a few inches near the device. Depending on the specific application, ultrasound devices can be more expensive and consume more power than other less expensive method. Calibrating them once they have gone out of calibrations requires special instrumentation not normally seen at a facility so the device will need to be returned to the manufacturer periodically for calibration.
Finally, to trouble-shoot a commercially available ultrasound unit for any issues will be challenging to the facility operator. The process for the facility operator will not be intuitively obvious because nothing touches the water. The operator will need to bring out the laptop, connect to the unit and run a diagnostic program. Again, it is not intuitive to make sure what is being done will fix the issues.
PROUDLY MADE IN THE U.S.A. 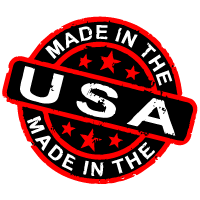
All of our liquid level controls and liquid level sensors are assembled right here in the U.S.A.
where we monitor every step of the process.
NOT SURE WHAT YOU NEED? JUST CALL BECAUSE WE’RE HERE TO HELP! 480-905-1892
We offer products comparable to the products offered by the above companies. See our website pages for further information on the products. The tradenames and trademarks in this page are owned by their respective companies or are the same name as the company. They are mentioned for comparison purposes only. They are in no way affiliated with System Dynamics, Inc or WaterLine Controls.