CAPACITIVE SWITCH FOR LIQUID LEVEL SENSING
Our Level Indicator sensors and switches can be implemented in a variety of industrial and commercial applications.”
They work by sending a 4-20mA output to the BMS or a control that will accept the 4-20mA.
Theory of Operation
A capacitive sensor consists of two probes which act as plates of a capacitor, and as the medium to be measured fills the space between the two capacitive plates; the capacitance changes due to the change in the dielectric of the medium between the plates. This “capacitor” is part of an oscillator circuit that governs the frequency of oscillation in an oscillator circuit in the probe and this frequency is dependent on the value of the capacitor.
The medium to be measured acts as the dialectic between the plates in the capacitor thereby changing the value of the capacitance and therefore the frequency of oscillation. It is mandatory that the dialectic constant of the medium be different than the dialectic constant of the material between the plates which is almost never a concern. The dielectric constant of all liquids is different than the dielectric constant of air. Air is the medium replaced when the liquid rises between the plates. Otherwise there would not be any change in the value of the capacitance. This frequency change is then measured and is then correlated to the level of the material.
Accuracy
This type of technology should be used as a water level indicator and not as a water level control device. There are several areas that can introduce errors in accuracy of the measurement. First, the probe must be calibrated for the characteristics of the medium being measured. This is usually not an issue since good capacitive probe sensor designs have incorporated a method of calibration for the particular medium being measured. Secondly, the dialectic constant of the material must not change over time or temperature. Unless the medium is a very exotic material, the change in the dielectric constant over time and/or temperature is very slight. Otherwise changes in the measured frequency can occur and give an error in the level measured. Third, if high accuracy is needed (smaller than a few percent), then high precision in the frequency measurement is required. A well-designed sensor assembly can easily achieve accuracies to less than 5%. Finally, the change in frequency is not a linear function so the level will increasingly become more sensitive to errors at one end of the measurement range. Again with proper design these areas of potential error can be minimized so that an accurate assembly can be produced.
Applications
This sensing method is used primarily to measure and demonstrate continuous graduations in liquid heights. For example, a range that indicates a change in level with 10% to 15% accuracy can easily be achieved. By using the industry standard of a 4 to 20mA output signal, interference from the surrounding industrial environment can be eliminated. This also provides an interface output that can be customized to the individual’s specific needs. This sensor type has particular use in the measurement of liquids that are corrosive; either acidic or caustic; or even flammable in nature. The probes (capacitive plates) can be manufactured from materials, or have protective coating applied, that will resist any environment in which they are placed. With the proper selection of probe materials, environments that are not only corrosive in nature but also at extreme temperatures can be manufactured. Capacitive devices are useful in confined areas as well.
Some areas that may find applications for capacitive probes are:
- Monitoring of the levels in tanks that contain acidic or caustic liquids.
- Maintaining required levels by interfacing the output of the probe to controlling pumps and/or valves.
- Providing measurements of levels for inventory requirements.
- Making measurements in environments that would preclude the use of other measurement methods.
Advantages
The capacitive type is very useful for measuring the level of harsh liquid environments. It can also be mounted within a small volume and thereby be used in areas restrictive in space. Generally the probes will be sealed against the environment to which they will be exposed, thus making them useful in mediums that would otherwise corrode or render other sensor types useless. The design of thesee sensors can be such that the output can be of any form that meets the requirements of the end user. They can be designed in a modular form so that when maintenance is required, it is easily accomplished at relatively low cost.
Disadvantages
Capacitive devices rely on the change of frequency to determine the liquid level. Since the dialectic constant is different for most liquids, a means of calibrating the sensor must be supplied and the sensor must be calibrated for each different liquid being measured. This generally is a one-time occurrence which is accomplished during the installation process. If high accuracy is required, then the stability of the design and the details of the calibration process must be carefully followed. These devices tend to be less accurate that other methods. They can be off as much as 10% or 15% of the overall volume depending upon the original design and calibrations.
PROUDLY MADE IN THE U.S.A. 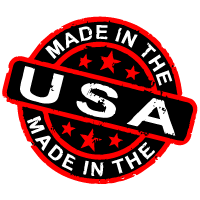
All of our liquid level controls and liquid level sensors are assembled right here in the U.S.A.
where we monitor every step of the process.
NOT SURE WHAT YOU NEED? JUST CALL BECAUSE WE’RE HERE TO HELP! 480-905-1892
We offer products comparable to the products offered by the above companies. See our website pages for further information on the products. The tradenames and trademarks in this page are owned by their respective companies or are the same name as the company. They are mentioned for comparison purposes only. They are in no way affiliated with System Dynamics, Inc or WaterLine Controls.